La maintenance prédictive a pour ambition d’améliorer la rentabilité de l’entreprise.
Cela en identifiant les problèmes qui menacent le bon fonctionnement de l’ensemble de la chaîne de production et en mettant fin aux maintenances inutiles.
Cet article a pour objectif de vous présenter un véritable navire amiral de l’industrie 4.0.
Maintenance prédictive : De quoi parle-t-on ?
La maintenance prédictive est une technique de maintenance industrielle moderne. Son but est d’aller au delà d’une surveillance de l’état des installations d’une usine. Elle permet d’anticiper les problèmes, et d’en identifier les symptômes. Plus agile que la maintenance préventive, cette nouvelle approche tend à s’imposer dans de nombreux secteurs industriels.
Quand la maintenance préventive a pour but d’anticiper les défaillances en planifiant à l’avance des activités de contrôle à intervalle régulier (à l’image de la révision de votre véhicule), la maintenance prédictive prend en compte les données propres à chaque installation, en temps réel et en continu. Cela permet donc d’éviter les dépenses inutiles telles que les remplacements de pièces détachées programmés à intervalles réguliers.
« Anticipation » est le maître mot de la maintenance prédictive.
Avec la maintenance prédictive, il est désormais possible de capter les données des machines en temps réel et de les analyser. Cela permet d’améliorer la rentabilité mais aussi la satisfaction client.
Précieuse pour l’entretien du matériel, la maintenance prédictive est surtout un moyen d’éviter une immobilisation imprévue de la chaîne de production. Elle permet de réduire le temps d’immobilisation des équipements, en diminuant de moitié le nombre de panne. Cette amélioration engendre une baisse de 3% à 5% sur les investissements de renouvellement. La maintenance prédictive est donc synonyme d’agilité et d’économies.
6 étapes vers un apprentissage progressif
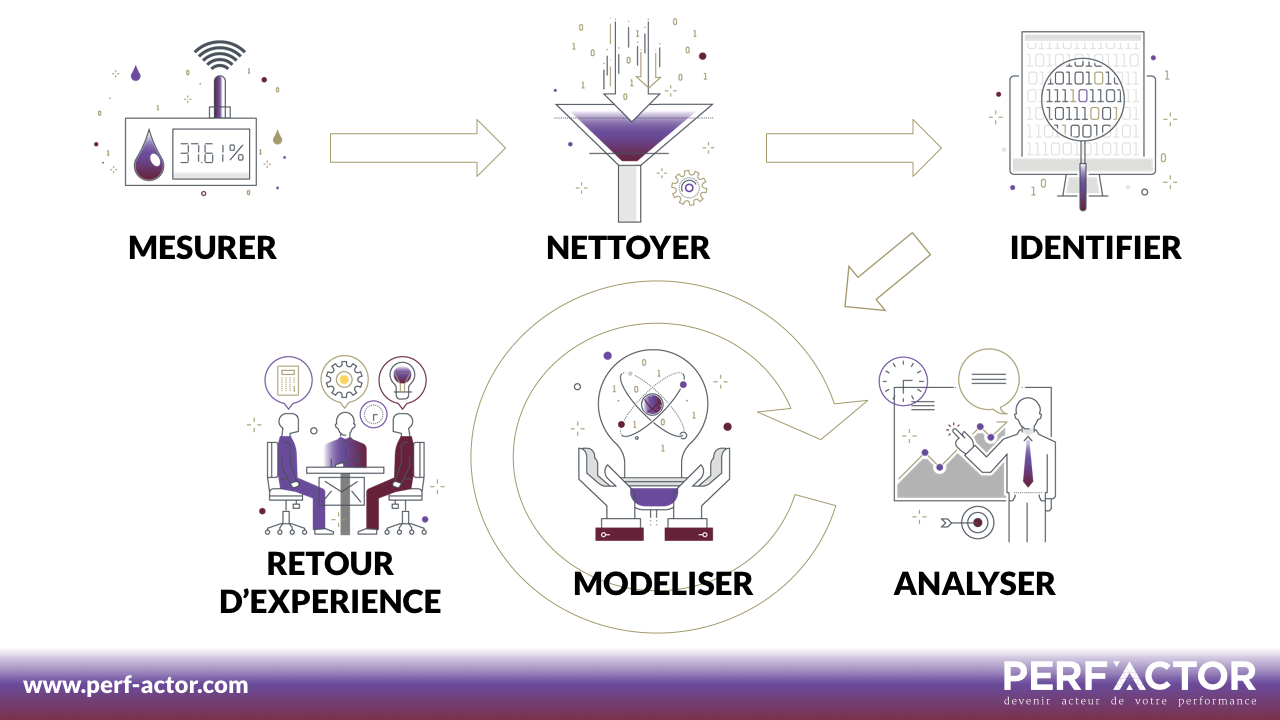
Etape 1 : Mesurer les informations

Afin de collecter des données de manière continue, il faudra équiper les installations de capteurs. Ces derniers permettent de collecter en temps réel l’information, et de la transmettre aux serveurs. Le choix de ces capteurs dépendra naturellement du type d’installation.
Etape 2 : Nettoyer les données
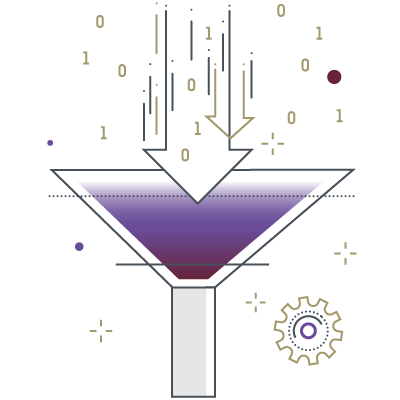
Les données brutes non transformées en sortie de capteur sont très rarement exploitables en l’état. De multiples raisons existent à cela : des éléments parasites biaisent les mesures de manière ponctuelle ou permanente, des doublons peuvent apparaître… Il est donc essentiel de filtrer et de trier les données pour qu’elles soient utilisables. Seules les données qui sont pertinentes du point de vue de la maintenance prédictive doivent être sélectionnées.
Etape 3 : Identifier les tendances
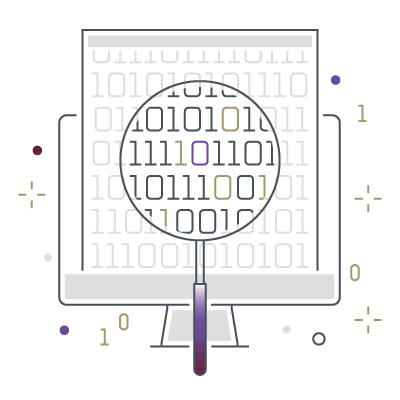
Une fois que les données sont nettoyées, il faut les analyser pour être en mesure de dégager des tendances vis à vis du comportement « normal » de l’installation ou des indices de la dégradation de ce fonctionnement. Les résultats de ces analyses permettront de poser les bases d’un modèle de maintenance prédictive pour cette installation.
Etape 4 : Modéliser le fonctionnement
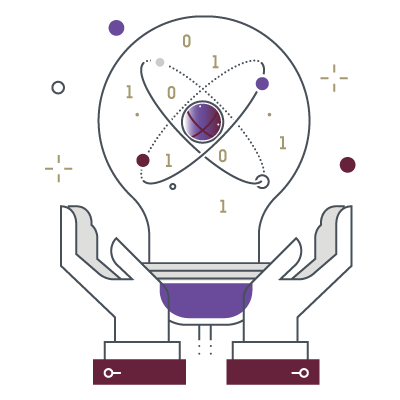
Votre installation industrielle sera modélisée grâce à des algorithmes et des schémas de panne spécifiques. La dégradation des machines pourra donc être anticipée en détectant les signaux avant-coureurs de dysfonctionnements plus sévères. Les pannes bien réelles sur la machine et les arrêts de production pourront être ainsi évités.
Etape 5 : Analyser les résultats
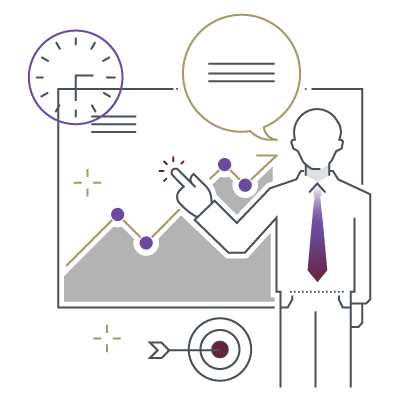
La maintenance prédictive se base sur l’exploitation des données historiques, il faut donc analyser régulièrement les résultats du modèle. Cette analyse permet de proposer des recommandations aux équipes de maintenance pour assurer une meilleure longévité du matériel.
Etape 6 : Améliorer grâce au retour d’expérience
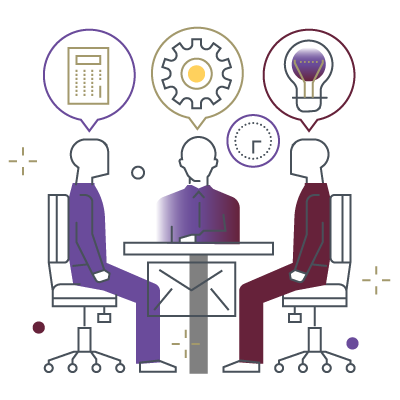
Certaines pannes sont facilement décelables, d’autres plus complexes à déceler. Le retour d’expérience est clé dans la démarche de la maintenance prédictive car il permet d’améliorer de manière continue le modèle. Au fur et à mesure des semaines et des pannes plus exceptionnelles, la modélisation prédictive se renforce et détecte des pannes de plus en plus complexes. Plusieurs corps de métier sont mobilisés pour transformer une panne subie en une panne détectable mais les bénéfices sont rapidement visibles.
Pour disposer des données à proximité de leur source, dans un espace centralisé et sécurisé, et éviter la latence des temps de traitement, une solution d’Edge Computing est particulièrement adaptée.
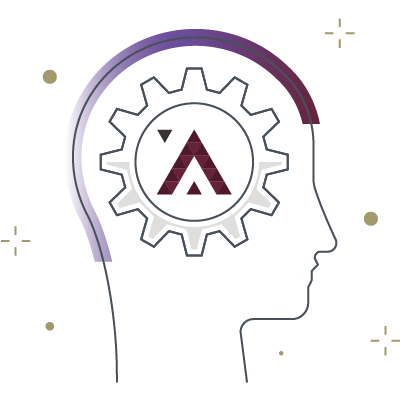
? Retour d’expérience
Il faut avoir conscience que la détection de pannes d’un point de vue modélisation et parfois différent du point de vue de l’humain. Un technicien de maintenance peut voir « à l’œil nu » que quelque chose ne va pas mais c’est difficilement transposable en l’état dans un algorithme.
On pourrait facilement imaginer une caméra et un algorithme de détection. L’environnement et les composants biaisent souvent les images (luminosité, taille du capteur en pixel…). Certaines pannes seront détectées de manière comparable entre ce que fait l’homme et l’algorithme, d’autres non.
C’est pour cela que le machine learning est d’un grand support pour la maintenance prédictive. Ces technologies vont permettre au système d’apprendre à reconnaître les nouveaux événements et les défaillances lorsqu’ils surviennent, et ce en temps réel et en continu. Il existe ici une véritable complémentarité à l’analyse humaine.
Alexandre Langlais, CEO PERF’ACTOR
Maintenance prédictive : Avantages et cas d’usage
Prévenir les dysfonctionnements
En détectant avec précision et en temps réel les anomalies et les symptômes d’usure des équipements, la maintenance prédictive permet d’anticiper les pannes. L’entreprise peut alors planifier des opérations d’entretien ou des réparations et donc maintenir sa production sans arrêts imprévus. Par exemple, les solutions de thermographie infrarouge (IR) vont permettre de détecter et de diagnostiquer des problèmes dans les équipements mécaniques, les systèmes électriques ou encore la tuyauterie de chaudières.
Inverser la logique de la maintenance
Autre avantage : l’agilité. En effet, la maintenance prédictive prend en compte le contexte d’utilisation de la machine et déclenche – si nécessaire – des actions de maintenance. Elle préserve ainsi le maintien des installations en condition opérationnelle. On dit que la maintenance prédictive permet de « passer d’une logique de flux poussés à une logique en flux tirés ». C’est-à-dire que c’est l’état actuel de l’actif qui déclenche ou non une intervention, et non un calendrier prédéfini. Dans la pratique, c’est le rôle des capteurs d’enregistrer les données d’utilisation et de les transmettre aux serveurs afin d’analyser en temps réel la performance et l’état des installations.
L’anticipation et l’agilité ont pour conséquence directe une amélioration de la rentabilité et de la performance grâce à des gains de coûts et de temps, bénéficiant aux résultats de l’entreprise :
- Réduction des arrêts imprévus de la production
- Diminution des stocks de pièces détachées
- Baisse des coûts de réparation et de maintenance
- Amélioration du taux de rendement global d’un équipement
- Qualité des produits accrue
La SNCF a d’ailleurs décidée de déployer des capteurs IoT sur l’ensemble de son réseau. Selon leur PDG Guillaume Pépy, cette stratégie de maintenance prédictive aura permis à la SNCF d’économiser près de 537 millions d’euros entre 2015 et 2020. Ces capteurs permettant aussi d’améliorer la sécurité en prévenant les incidents mineurs et en évitant qu’ils ne deviennent plus graves.
Il est important de noter que la plupart des entreprises disposent déjà d’une instrumentation pouvant être utilisée pour le suivi des performance et être complétée par des capteurs IoT peu chers, afin d’atteindre les exigences de la maintenance prédictive.
Autre avantage, la maintenance prédictive renforce et enrichie la communication entre les techniciens et les analystes.
Une qualité de service améliorée
Si on se place du côté des fournisseurs d’installations industrielles ou de services de maintenance, cette nouvelle technologie permet d’améliorer la satisfaction client. Car le fournisseur n’intervient que lorsque des signaux émis par une machine reflètent une panne probable à court terme. Prenons l’exemple de Schindler ou ThyssenKrupp qui ont décidé de mettre en place des capteurs sur leurs ascenseurs. Les données concernant la température collectées et analysées permettent d’ « identifier le nombre maximum d’ouvertures de portes avant la quasi-certitude d’une panne » . Leurs clients ont enfin la certitude d’avoir un ascenseur qui fonctionne en permanence.
Les principaux outils de la maintenance prédictive sont les suivants :
-
l’imagerie thermique fonctionnant par infrarouge
- l’analyse de la vibration permettant d’identifier rapidement les causes d’usure
- la détection des ultrasons mettant en évidence les fissures ou les mauvaises soudures
- l’analyse des liquides permettant de détecter les fuites et la présence de particules ou de mesurer les niveaux d’huile
- les tests d’émission (des gaz résiduaires par exemple) qui en disent long sur l’état des machines et mettent en lumière votre démarche respectueuse de l’environnement
Aussi, la mise en place d’un jumeau numérique permet de bénéficier de tous les avantages de la maintenance prédictive.
Quelle stratégie d’entreprise utiliser pour la maintenance prédictive ?
Avant de déployer cette technologie, il faut s’interroger sur sa pertinence et les gains potentiels. Car l’investissement initial est significatif :
- équipements de diagnostic et de surveillance
- formation du personnel de l’usine
- gestion des données
- éventuelle embauche ou formation d’analystes (data analyst, data scientist…)
Aussi, on privilégiera toujours une maintenance préventive dans des situations où il existe un risque de vie humaine.
Comme tout changement d’envergure, l’utilisation de technologies digitales complexes demande une nouvelle maîtrise à acquérir, l’implication et la collaboration des équipes.
La maintenance prédictive fonctionne très bien si elle est ciblée. Elle est beaucoup plus complexe quand l’entreprise veut l’appliquer à grande échelle.
Les entreprises font souvent l’erreur de se concentrer sur le résultat sans avoir réfléchi en amont à la stratégie adaptée à leur dimension. La connaissance des enjeux métiers est également au cœur d’un déploiement réussi de la maintenance prédictive.
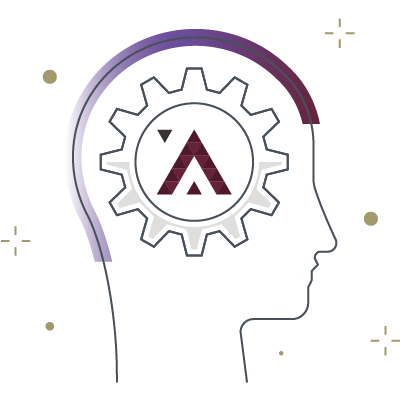
Afin de s’assurer de l’alignement stratégique de votre démarche prédictive, il est recommandé de suivre les étapes suivantes :
- S’interroger sur la pertinence du projet par rapport à la stratégie de l’entreprise et en mesurer les gains et la rentabilité à long terme.
- Faire un audit de la ligne de production, des différents équipements, des ressources humaines et des compétences disponibles et à prévoir.
- S’assurer de la connectivité de bout en bout entre les capteurs et le serveur back-end : la fiabilité de cette connexion indique le niveau de confiance à accorder aux prédictions du système.
- Vérifier que les données collectées sont en phase avec les objectifs recherchés.
- Déterminer les modèles de prédiction de défaillances en combinant l’analyse de données, l’avis des experts métier et l’expérimentation de ces modèles.
L’utilisation la plus efficace de la maintenance prédictive dépend de la manière dont vous l’appliquez pour vous aider à prévoir et éviter des pannes et non pas simplement d’y réagir. Aussi, il est intéressant de faire appel à une solution évolutive qui permette de facilement passer à une dimension supérieure.
Alexandre Langlais, CEO PERF’ACTOR
Un impact positif sur votre performance 4.0
Au vu de ses nombreux avantages (ROI, performance, agilité…), cette technique moderne de maintenance industrielle s’est imposée dans les usines.
Les entreprises ont compris que grâce à la maintenance prédictive, elle pourraient réduire les pannes, éviter les imprévus et les immobilisations de la chaîne de production.
Conséquence directe, le service rendu au client est amélioré : la maintenance prédictive participe à la livraison des produits dans le respect de la qualité, des prix et des délais convenus.
En 2016, les investissements en maintenance prédictive représentaient déjà un montant de 9,1 milliards de dollars au niveau mondial (source : ABI Research). Aussi, selon le cabinet McKinsey, la maintenance prédictive permettra aux entreprises d’économiser 630 milliards de dollars d’ici 2025.
A l’heure de l’industrie 4.0, la maintenance prédictive s’impose comme un des principaux leviers de la performance industrielle des entreprises.
Prêt pour passer à la maintenance prédictive ?
✔ Un expert en pilotage de la performance à votre écoute pendant 45 minutes.
✔ Une analyse à 360° pour qualifier votre niveau de maturité sur 12 dimensions
✔ Des conseils personnalisés pour booster votre compétitivité
✔ Des cas concrets adaptés à votre business
✔ Une synthèse visuelle et synthétique dans votre boîte email
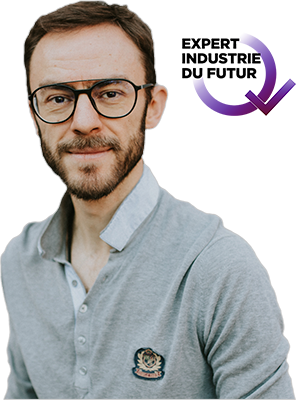
Alexandre Langlais, CEO PERF'ACTOR
✔ Une définition claire et précise de ce qu’est l’IoT industriel
✔ Quels bénéfices attendre de l’IoT industriel
✔ Une vue d’ensemble des technologies embarquée dans l’IoT
✔ Des applications concrètes pour se projeter plus facilement
✔ Quelles bonnes pratiques appliquer pour se transformer plus rapidement
✔ Les menaces qui pèsent sur les projets IIoT que vous allez mettre en place